Electric kilns: How an old technology is key to our climate future
A lot of what we do at Heirloom is on the cutting-edge, but when it comes to one key aspect of our technology, we’re using something that has been around for a century: the electric kiln.
Electric kilns have been around since the 1920s, and are readily available and widely used across industries. They bring a number of advantages over fossil-fuel-powered kilns. The biggest advantage is that electric kilns consistently achieve higher thermal efficiency than fossil-powered kilns. Since electric kilns do not need to burn fuel to generate energy, there are no energy losses associated with heating the fuel to its combustion temperature — in other words, there is no energy lost in the combustion process. This also allows more precise and consistent temperature control. Electric kilns also do not produce harmful emissions from combustion, like carbon monoxide or nitrous oxides.
While kilns are often used to make things — like ceramics, glass, or steel — we’re using this technology to break apart limestone. By heating limestone in an electric kiln, we can break down the material into its constituent parts: calcium oxide (CaO) mineral and CO2 gas. The resulting calcium oxide really wants to take up more CO2 to return to a natural limestone state, rendering it highly reactive with CO2. This destruction and recreation of limestone is what allows us to continuously sponge CO2 from the atmosphere, before permanently and safely storing it in building materials or underground wells.
Heirloom uses electric kilns for several reasons — all focused on creating a low cost, clean, and sustainable direct air capture process. The electric kiln enables us to circumvent the 40–50% of emissions that are associated with heating the kiln to temperature, as well as produce a pure stream of CO2 directly from the kiln without additional, energy-intensive, post-calcination separation processes. This also allows the kiln to avoid greenhouse gas emissions associated with upstream procurement of natural gas and other fossil energy sources, as well as avoid other, non-CO2 pollutants that result from combusting fossil energy.
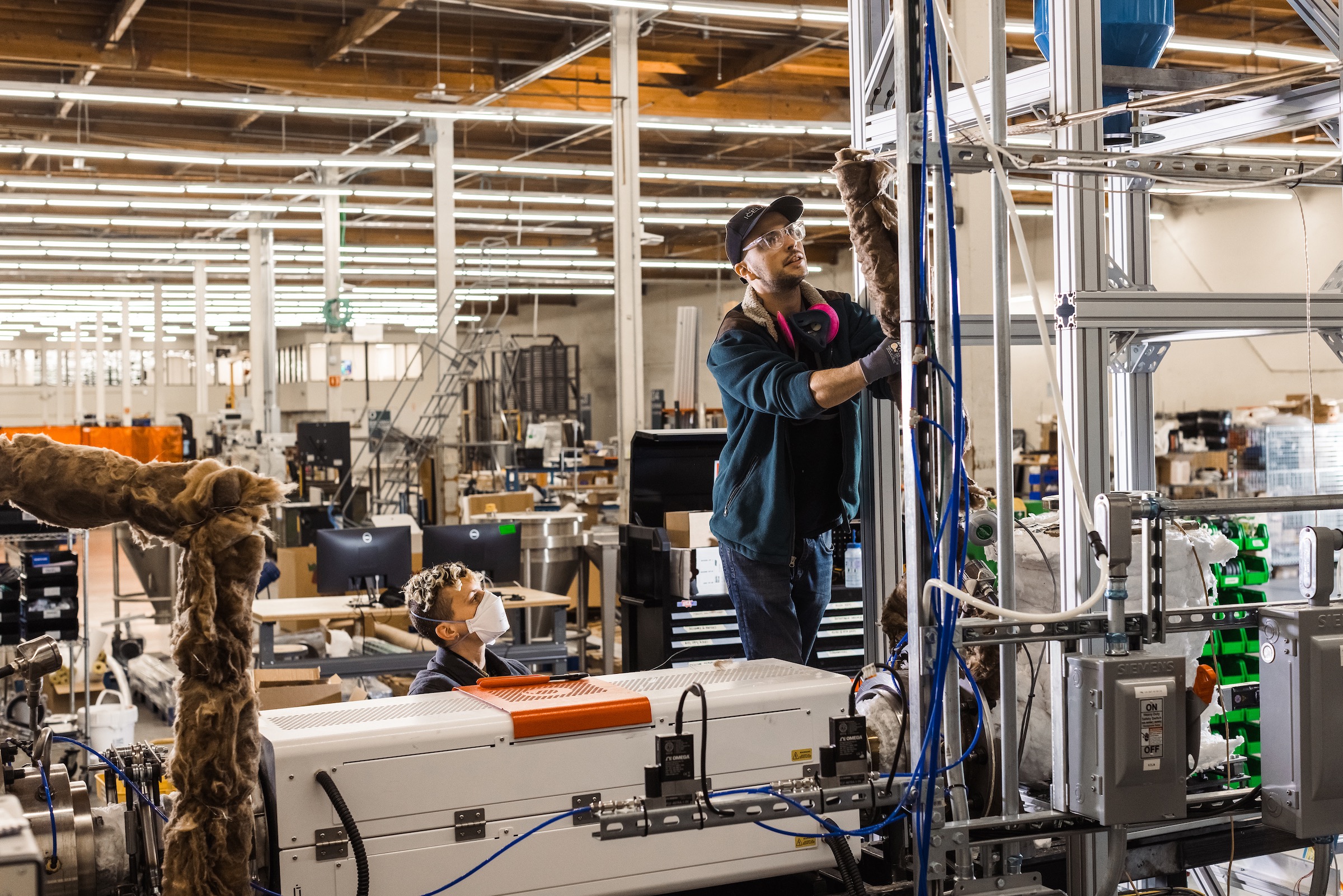
While electric kilns have been around for a century, the last couple of decades have been ripe with innovation and we are finding new and innovative ways to improve and apply the technology to combat the climate crisis. Although simple, some improvements have a big impact — such as improved healing elements with even higher efficiencies and new materials for insulation to prevent thermal losses to the environment.
Other innovations have changed the way we think about and use electric kilns. In Germany, the government is backing the development of a large-scale electrically heated steam cracker furnace — a technology that will enable the production of value-added chemicals with renewable energy, rather than with fossil fuels as is done today. And in Finland, a startup has developed an electric kiln that can reach 1700°C, enabling it to replace fossil-fired furnaces and kilns with electric heating in industrial processes.
Other innovations seek to create more modular scale systems that can be rapidly manufactured and allow for ease of installation at an industrial site — a key advantage of electrified technologies. Companies like Leilac are creating modular, indirectly-heated reactors to decarbonize the cement industry. Since heavy industry accounts for roughly a quarter of global emissions — a large portion of which comes from industrial heating and fossil-powered reactors — electric kilns can also play a huge part in decarbonizing multiple sectors of our economy.
Demand for electric kilns is heating up (pun intended) given the increasingly important role they’ll play in stabilizing our climate — both from a decarbonization and carbon dioxide removal perspective.
Read More
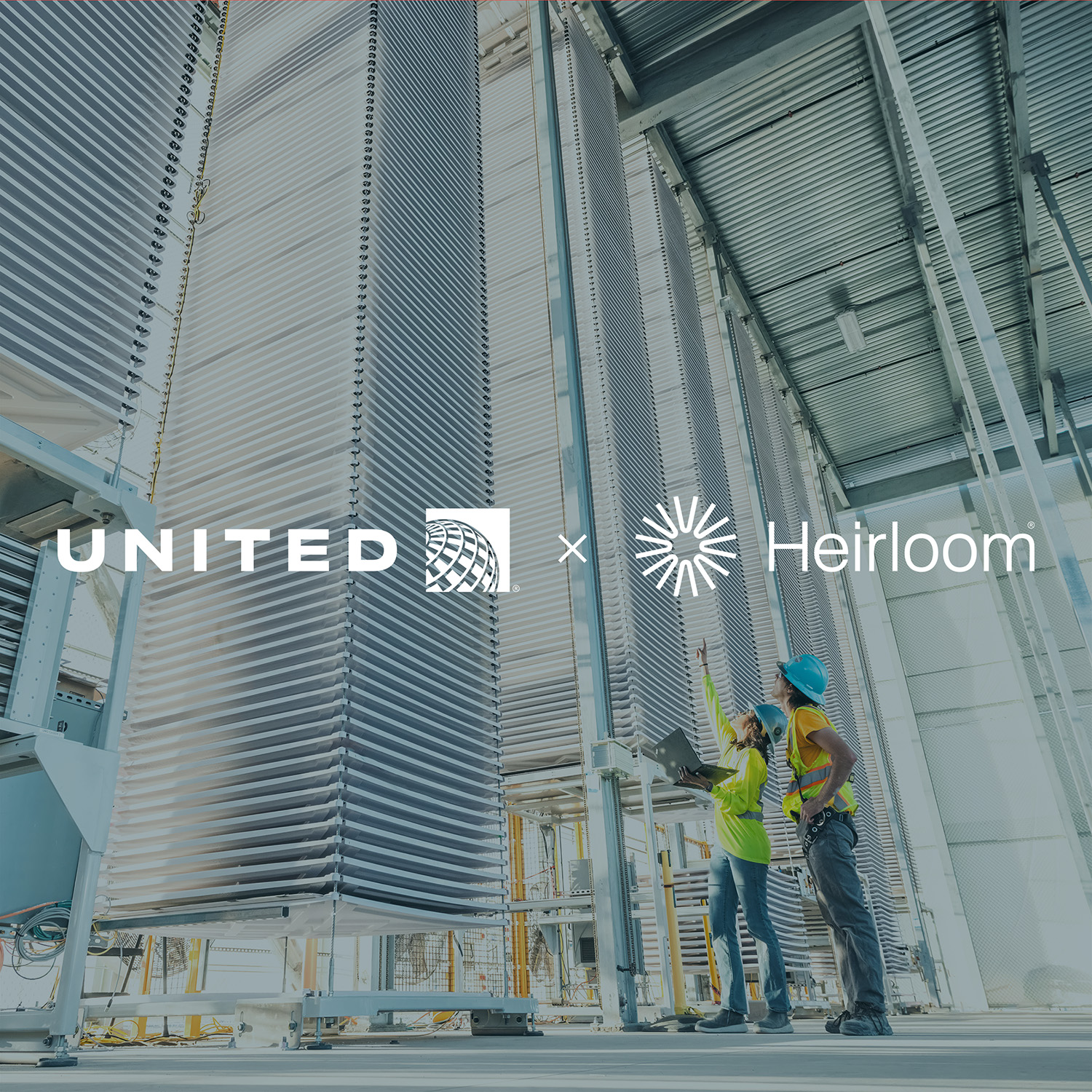
Working with United Sustainable Flight Fund to Accelerate Aviation’s Path to True Net Zero
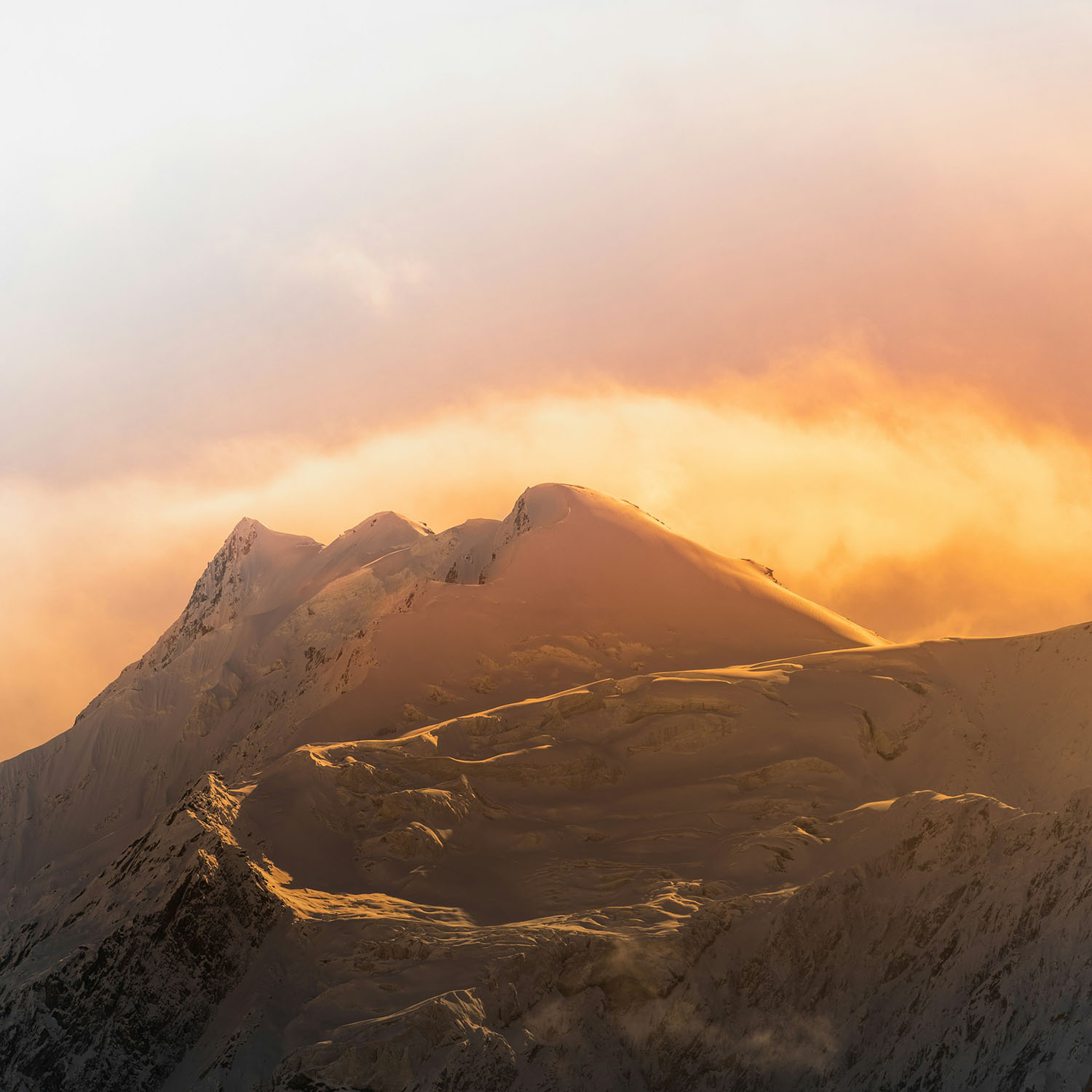
As we conclude this pivotal year, we remain committed to removing billions of tons of carbon dioxide from the air
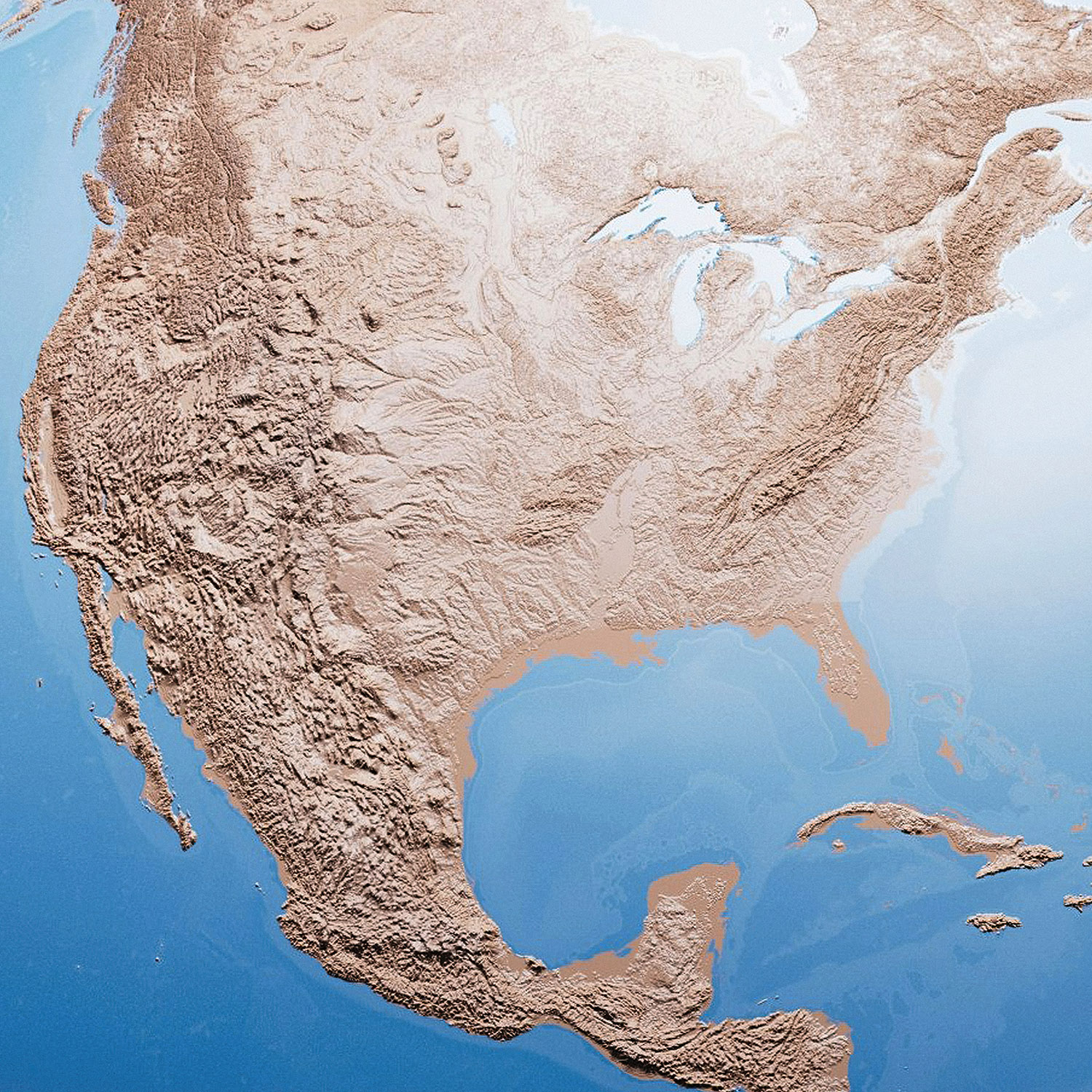